Tres opciones para el desbaste y nivelación de superficies de pisos de concreto
El primer tipo:
El primer paso para pulir y nivelar la superficie del piso de concreto es usar una discos de resina diamantados de calibre 50. Estos discos están diseñados para eliminar activamente las imperfecciones e irregularidades de la superficie, lo que da como resultado una superficie más uniforme. Esta etapa inicial de pulido aproximado es fundamental para abordar cualquier protuberancia, depresión u otra irregularidad notable en el concreto.
Después de completar el desbaste inicial, continúe usando discos de desbaste diamantado de resina de 100# y 200#. Estos discos de grano más fino pueden refinar aún más la superficie, suavizando los parches ásperos restantes y creando una apariencia más pulida. Este proceso de lijado paso a paso garantiza que el suelo de hormigón se nivele y alise gradualmente, dando como resultado un acabado de alta calidad.
Este método es particularmente eficaz para tratar pisos desgastados de concreto esmerilado o pisos de travertino relativamente planos que han sido pulidos y pulidos pero que se han vuelto viejos y manchados con el tiempo. Este tipo de superficies suelen requerir un minucioso proceso de lijado y nivelación para restaurar su apariencia y funcionalidad.
El segundo tipo:
El segundo tipo de pulido de superficies rugosas consiste en utilizar discos de desbaste diamantado de resina de 100# o 150# para pulir la superficie de hormigón relativamente plana previamente tratada. Este método es particularmente eficaz para eliminar contaminación superficial, marcas de arrastre de hardware o pisos corroídos por agentes ácidos. El proceso comienza lijando cuidadosamente las imperfecciones e irregularidades de la superficie para crear una base más uniforme y nivelada para el procesamiento posterior.
Una de las principales ventajas de utilizar discos de desbaste diamantado de resina para el pulido de superficies rugosas es su capacidad para eliminar eficazmente las imperfecciones de la superficie manteniendo el control del proceso de pulido. El tamaño de grano 100# o 150# es moderadamente agresivo, lo que lo hace adecuado para abordar varios tipos de irregularidades de la superficie sin causar daños indebidos al concreto.
Además, después del proceso inicial de desbaste, la superficie tratada puede someterse a pasos adicionales, como la penetración del endurecedor, esmerilado adicional y pulido para cumplir con requisitos funcionales y de proceso específicos. Este enfoque integral garantiza que la superficie del suelo de hormigón no sólo sea lisa sino que también esté lista para el procesamiento posterior, lo que da como resultado un acabado similar a un espejo.
El tercer tipo:
El tercer tipo de pulido y nivelación en bruto implica el uso de placa de molienda trapezoidal más grueso, generalmente usando grano 16#, 30# o 50#, para abrir los poros de la superficie del concreto. Este método es ampliamente favorecido por su efectividad para crear pisos de concreto lisos y uniformes, lo que lo convierte en una opción popular para aplicaciones prácticas. Al pulir la superficie hasta lograr un alto nivel de suavidad, se sientan las bases para los pasos de pulido posteriores para lograr el acabado deseado para la satisfacción del cliente.
Una de las principales ventajas de utilizar un bloque de pulido con hoja de metal más grueso es su capacidad para abrir los poros de la superficie del hormigón, lo que permite una mejor adhesión y penetración de tratamientos posteriores. Este proceso no sólo alisa la superficie sino que también la prepara para un mayor refinamiento, asegurando que el piso de concreto esté listo para la siguiente etapa de pulido y acabado.
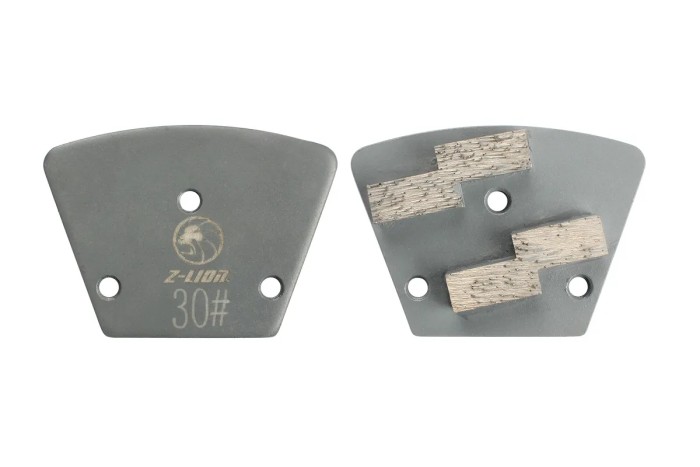
La elección correcta de las zapatas abrasivas para desbaste, nivelación y desbaste:
Al desbastar y nivelar suelos de hormigón, el éxito del proceso no sólo depende de la presión de pulido del disco abrasivo mecánico, sino también de la fuerza de corte del bloque abrasivo con cabeza metálica. El filo y la resistencia al desgaste del cabezal de corte, así como el tamaño de las partículas y la uniformidad de las partículas de diamante en el bloque abrasivo, desempeñan un papel crucial para obtener los mejores resultados.
La fuerza de corte del bloque de esmerilado con cabezal cortador de metal es un factor clave en el desbaste y nivelación de pisos de concreto. Esta fuerza se ve directamente afectada por el filo y la resistencia al desgaste del cabezal cortador, que a su vez está determinada por el tamaño y la uniformidad de las partículas de diamante en el bloque abrasivo. Cuanto más gruesas y uniformes sean las partículas de diamante en el bloque de molienda, más nítidas y mayor será la eficiencia de molienda. Por el contrario, las partículas de diamante pasivadas reducen la eficiencia del rectificado. Por lo tanto, la selección del bloque abrasivo y la malla del disco abrasivo debe adaptarse de acuerdo con las condiciones específicas del sitio para garantizar la mejor fuerza de corte y eficiencia.
Además del tamaño y la uniformidad de las partículas de diamante, también es decisiva la elección de la matriz del bloque abrasivo como soporte para las partículas de diamante. La matriz está compuesta por varios polvos metálicos o una mezcla de polvos metálicos y resina, recubierta con partículas o polvo de diamante. La composición y calidad de la matriz afectan significativamente el rendimiento general y la durabilidad del bloque abrasivo. La elección de la matriz adecuada garantiza una retención y distribución efectiva de las partículas de diamante, lo que en última instancia contribuye a la fuerza de corte general y a la eficiencia durante el desbaste y la nivelación.